- Premium Efficiency IE3 motors for greater energy savings
- Long-term reliability with wastewater-designed impellers
- Greater energy savings gives smaller CO2 footprint
- Excellent rag handling for minimized downtime
- Sustainable in manufacturing and operation
Submersible sewage pump type ABS XFP
Submersible pumps for greater energy savings
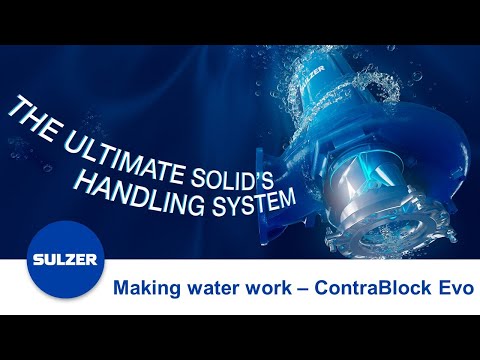
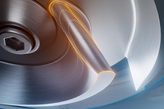

- Clean water and wastewater
- Sewage containing solids and fibrous material
- Sewage with sludge and high rag content
- Industrial raw water
- Municipal combined sewage and storm water systems
- Premium Efficiency IE3 motors in acc. with IEC60034-30 (from 1.3 - 550 kW in 50 Hz and 2.7 - 830 hp in 60 Hz)
- ContraBlock family impeller type single and multivane
- Vortex impeller type family
- Closed and skew type impellers
- Explosion-proof version as option (ATEX, FM or CSA)
- Closed cooling system (PE1-2)
- Closed-loop cooling system - standard in PE6 (PE3-PE5 optional)
- Temperature rise according to NEMA Class A up to 110 kW and Class B above
- Class H (140°C) insulation
- Condition monitoring (temperature, water ingress)
- 100'000 hours bearing life (50'000 hours on PE1-2)
50 Hz | 60 Hz | |
Pump sizes | 80-800 mm | 80 to 800 mm / 3.2 to 32 in |
Capacities | up to 2'400 l/s | up to 2’500 l/s / 39’600 USgpm |
Heads | up to 80 m | up to 95 m / 310 ft |
Power | 1.3 to 550 kW | 2 to 620 kW / 2.7 to 830 hp |
No of poles | Power P2 (kW) | ||||||
PE1 | PE2 | PE3 | PE4 | PE5 | PE6 | PE7 | |
2 |
50 Hz: 3-4 60 Hz: 4.5 |
50 Hz: 5.5-11 60 Hz: 8-12.5 |
50 Hz: 15-25 60 Hz: 18.5-30 |
50Hz: 35-42 60 Hz: 43-54 |
- | - | - |
4 |
50 Hz: 1.5-2.9 60 Hz: 2.2-3.5 |
50 Hz: 4-9 60 Hz: 4.5-10.5 |
50 Hz: 11-30 60 Hz: 13-35 |
50 Hz: 22-45 60 Hz: 25-52 |
50 Hz: 55-110 60 Hz: 63-125 |
50 Hz: 132-250 60 Hz: 150-335 |
- |
6 |
50 Hz: 1.3 60 Hz: 2 |
50 Hz: 3 60 Hz: 3.5 |
50 Hz: 9-22 60 Hz: 9-25 |
50 Hz: 18.5-37 60 Hz: 21-43 |
50 Hz: 45-90 60 Hz: 52-104 |
50 Hz: 110-200 60 Hz: 125-220 |
50 Hz: 250-550 60 Hz: 290-620 |
8 |
50 Hz: - 60Hz: 12 |
50 Hz: 15-30 60 Hz: 17-35 |
50 Hz: 37-75 60 Hz: 43-86 |
50 Hz: 90-132 60 Hz: 104-150 |
50 Hz: 160-450 60 Hz: 185-500 |
||
10 |
50 Hz: 30-55 60 Hz: 35-63 |
50 Hz: 75-132 60 Hz: 86-150 |
50 Hz: 160-350 60 Hz: 185-415 |
||||
12 |
|
50 Hz: - 60 Hz: 86-150 |
50 Hz: 160-300 60 Hz: 185-350 |
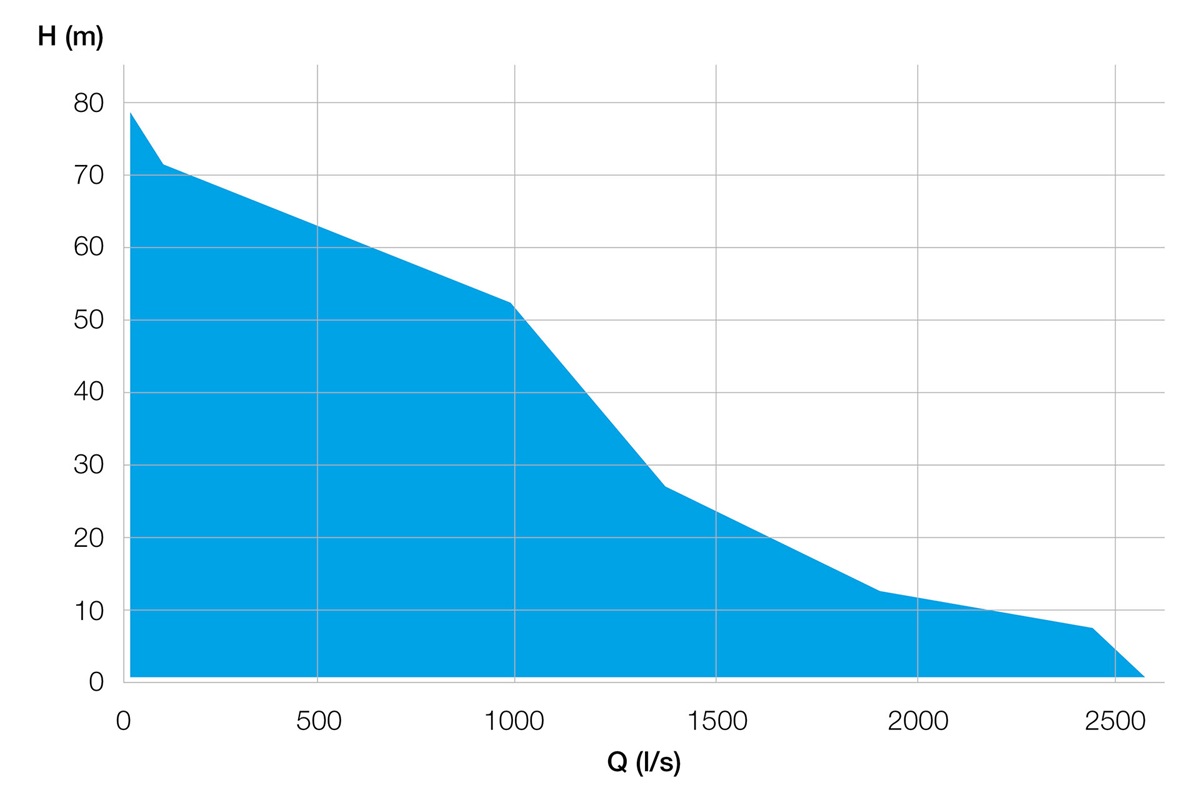
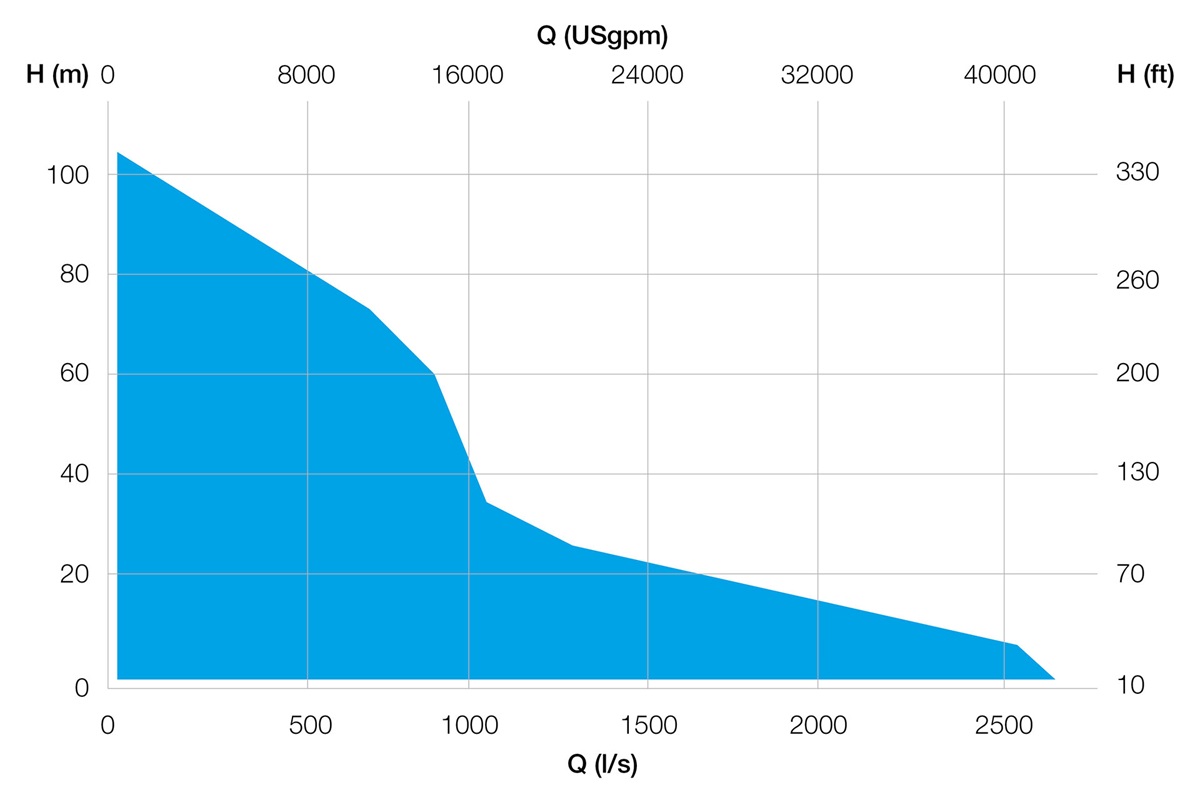
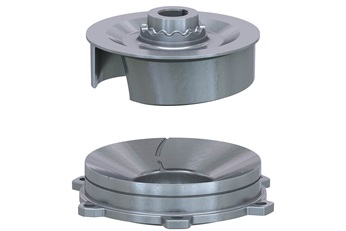
ContraBlock Plus
Specifically engineered to handle tough challenges of high rag and solid content, a consequence of water conservation efforts.
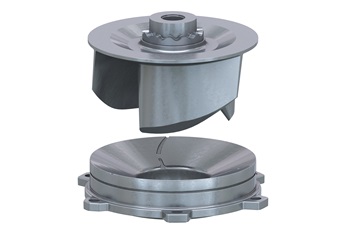
ContraBlock Evo
The next innovative step to improve non-clog behavior handling higher rag and solid content. The ContraBlock Evo uses unique vane geometry and Pulse-Out technology for highly efficient solids passage.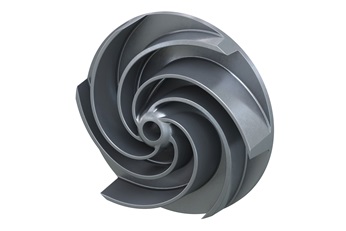
Vortex
Featuring a large passage for solids, vortex impellers are perfect for pumping liquids with gas, sand, or low flow/high head requirements. They're commonly used in small pumping stations in rural areas due to their clog-resistant nature.
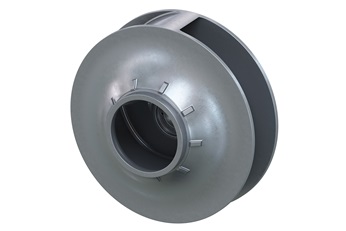
Channel
Channel impellers are perfect for liquids without fibers. For wastewater with fibers, their suitability depends on the pump size and can be determined using Sulzer's ABSEL wastewater pump selection program.
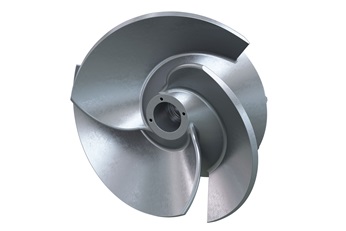
Skew
Skew impellers excel in handling sewage at large pumping stations. Their semi-open, mixed-flow design combines the advantages of axial and centrifugal impellers, allowing for a large solids passage.
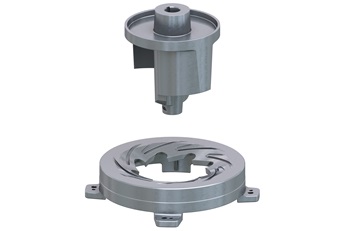
Chopper
Chopper impellers are specifically designed to address the challenge of long or bulky waste materials by cutting them into manageable pieces.
Brochures
Technical articles
-
A lifetime of efficiencypdfLanguages:
-
Keeping wastewater arteries clearpdfLanguages:
Case studies
Data sheets
Dimension drawings
Installation manuals
Brochures
Technical articles
-
A lifetime of efficiencypdfLanguages:
-
Keeping wastewater arteries clearpdfLanguages:
Case studies
Data sheets
Dimension drawings
Installation manuals
-
Sulzer’s turnkey pumping station reduces energy costs by 40%Sulzer has completed the first in a series of wastewater pumping stations for a Danish municipality. Replacing a pre-existing facility, the new station offers twice the capacity of the old one, while its highly efficient, horizontally mounted XFP pumps have cut energy demand by 40 percent.
-
Building flood defenses to stand the test of timeLooking ahead at rising sea levels, water utilities in low-lying areas need to be planning how to handle increased risks of flooding. In Denmark, defenses in the Ringkøbing Fjord have been bolstered by the installation of two new pumping stations, which have been designed and equipped by Sulzer. The new facilities will help to protect the town and the surrounding countryside for the next 40 years and far beyond.
-
Pump impeller technology against blockagesSeptember 15, 2020Pump blockage is a growing and costly issue for wastewater companies. Choosing a pump designed specifically to meet the challenges of frontline operation in sewage networks can dramatically cut downtime and minimize asset lifetime costs.
-
XFP pump with Contrablock hydraulics limits cloggingThe Pernes Les Fontaines wastewater treatment plant in France, part of the Rhône-Ventoux mixed water union, treats a daily pollution of 12’000 population equivalents.
-
Sulzer Pumps reduce downtime at water utilityWinslow Township is the largest town in Camden County, NJ, USA. The town runs its own in-house water and sewer utility. The pumps installed in the two pumps stations - Ivy Hall and Victoria Manor - often clogged and experienced reliability issues. Even partially clogged pumps greatly reduce energy efficiency. Customer callout time and overtime to service these stations was very high.
-
Sulzer delivers pumps for the largest water construction project in EuropeAs part of the reconstruction of the Emscher river and its tributaries, a multistory underground facility is being built in Gelsenkirchen at the river Hüller Bach. This project comprises three reservoirs, two rainwater treatment plants and three pumping stations. The excavation has a diameter of around 33 meters. Numerous and sometimes very large pumps are needed because of the large quantities of water. Sulzer delivered the submersible pumps for the plant that is expected to be operational in 2020.
-
Submersible pumps run at optimum hydraulic efficiencyTo reduce the carbon footprint, the Avebe wastewater treatment plant in Netherlands replaced their existing radial pumps by Sulzer’s stainless steel XFP submersible sewage pumps with Contrablock Plus impellers and Premium Efficiency IE3 motors.
-
Installation of submersible sewage pumps gives substantial energy savingsThe village Sluis in the Netherlands is a popular touristic attraction and therefore the municipality cannot afford any blockages in the wastewater transportations. The installation of Sulzer submersible sewage pumps gave substantial energy savings.
-
Proven expertise in dewatering pumps rentalNeptune is a company specialized in the rental and sale of pumping equipment for clean water, wastewater and water loaded to industry, construction and communities. Its rental fleet includes 90% of dewatering pumps and 10% of sewage pumps. Neptune has already trusted Sulzer as a supplier for many years and has ordered several dewatering and sewage pumps.
-
Sulzer’s submersible sewage pump offers unmatched blockage resistanceKaimai Valley Services in New Zealand had a pump station that was blocked with soft solids, rags, etc. on average 1-2 times per week. The pump was replaced by a Sulzer submersible sewage pump type ABS XFP and the blockages stopped.
-
Sulzer pumps improve wastewater treatment in a sugar and bioethanol plantTereos is the leading sugar and alcohol producer in the Czech Republic. The factory trusts Sulzer’s equipment for its demanding wastewater applications, like the XFP sewage pumps with Contrablock Plus impellers and Premium Efficiency IE3 motors.
-
Sulzer secures contract for Danish climate protection schemeNine Sulzer pumps are set to play a key role in new flood defenses around the town of Ringkøbing. Danish water utility Ringkøbing-Skjern Forsyning A/S has selected Sulzer as the primary pump supplier for a major flood defense project.
-
Driving up efficiencyThe adoption of electric vehicles across the world is increasing rapidly and this demand needs to be matched by the supply of batteries. As new processing plants and manufacturing facilities are constructed, it is important that they employ the latest in pumping technology to ensure optimum reliability and efficiency. Read the article.
-
Tackling wastewater challenges system-wideBlockages in municipal wastewater systems are costly for utilities, inconvenient for users and potentially harmful for the environment. This increased stress on the system leaves the operators to find a smarter approach to ensure network-wide reliability.
-
Monster keeps major infrastructure project on trackA Sulzer Channel Monster has been a lifeline for a large-scale wastewater treatment project in Vác, Hungary
-
A lifetime of efficiencyElectric motors in industrial applications, including those used in pumping systems, consume 30 to 40 percent of the world’s electricity. For the past two decades, equipment manufacturers, users and regulators have been tackling excessive energy consumption.
-
Ensuring the right mixSulzer technology is playing a key role in Energiefabriek West, an innovative bio-power scheme in the Netherlands. The Rivierenland Water Authority in the Netherlands is investing in new infrastructure to improve the performance of its wastewater treatment systems while also reducing its impact on the environment. The utility is aiming to become energy neutral by 2030, and Sulzer technology is helping it to realize this goal.
-
Greening the desertThe plant, which was officially inaugurated by the country’s president Abdel Fattah El Sisi in April 2020, will produce enough clean water to irrigate 70’000 acres (283 square kilometers) of agricultural land.
-
Sulzer’s analysis of wastewater pumping stations enables Spanish municipality to optimize performance and reduce costsIn the City of Vilagarcía de Arousa in North-western Spain, problems with the sewage network were leading to pollution events and a EUR 200’000 annual maintenance bill. To resolve these issues, the city council partnered with experts from Sulzer’s service center in nearby Vigo.
-
Smarter control of wastewater pump networks transforms performance, reliability and cost-efficiencyData flows faster than water, providing a stream of optimization opportunities. The latest in control technology allows pumping stations and wastewater treatment facilities to talk to each other, providing a better picture of real-time conditions and enabling smarter, more proactive management of the whole network.
-
Case studiesWherever fluids are pumped, mixed, controlled or applied, we are there. See how our solutions create value for customers and learn how we can make your pumping and mixing processes more efficient and profitable, safeguarding your production and ensuring lasting reliability.
-
Commercial waste disposal from toiletsCommercial wastewater from toilets comprises all sewage water flushed from toilets on commercial, industrial or public properties.
-
Network pumping stationNetwork pumping stations collect municipal wastewater from residential homes and communal schemes. Installed in dry or wet wells, the pumps deliver the effluent to a terminal pumping station. Since most pumping stations are not equipped with screens, the pumps must cope with difficult materials such as fibrous sanitary and packaging items.
-
Terminal pumping stationTerminal pumping stations receive municipal wastewater from network pumping stations. Installed in dry or wet wells, the pumps forward the medium to a treatment plant for final purification. Due to the lack of screens at most pumping stations, difficult materials such as fibrous sanitary and packaging items are a constant threat to uptime.
-
Inlet pumping stationInlet pumping stations are somewhat similar to large terminal pumping stations. Depending on the depth of the incoming sewer, the lifting heads can range from around 2 up to 30 meters. To prevent hydraulic shock loads, which negatively impact the biological process, the stations often make use of variable-speed drives and/or several pumps in parallel.
-
Outlet pumping stationsOutlet pumping stations are required when the level of the treatment plant is lower than that of the receiving water. This is especially true when discharging into a river, which can rise during heavy rain or flood periods, or into the sea, where the level varies with the tide. Outlet pumping stations may also be needed to compensate for increasing frictional losses in the outgoing pipe at high flows, for example in long sea outfall pipes.
-
Return of activated sludgeOutlet pumping stations are required when the level of the treatment plant is lower than that of the receiving water. This is especially true when discharging into a river, which can rise during heavy rain or flood periods, or into the sea, where the level varies with the tide.
-
Dewatering in tunnelingA tunnel construction is a complex worksite were many different variables need to be taken into consideration, flooding is one of them. Our drainage and sludge submersible dewatering pumps are lightweight, portable and start when you plug them in.
-
Mine water managementSulzer offers a comprehensive portfolio of pumps and process equipment for abrasive and corrosive environments in mine water management applications.
-
Service centers for water, wastewater and dewateringFind the service center nearest to you. With more than 100 service centers worldwide, we are always close to the customer.
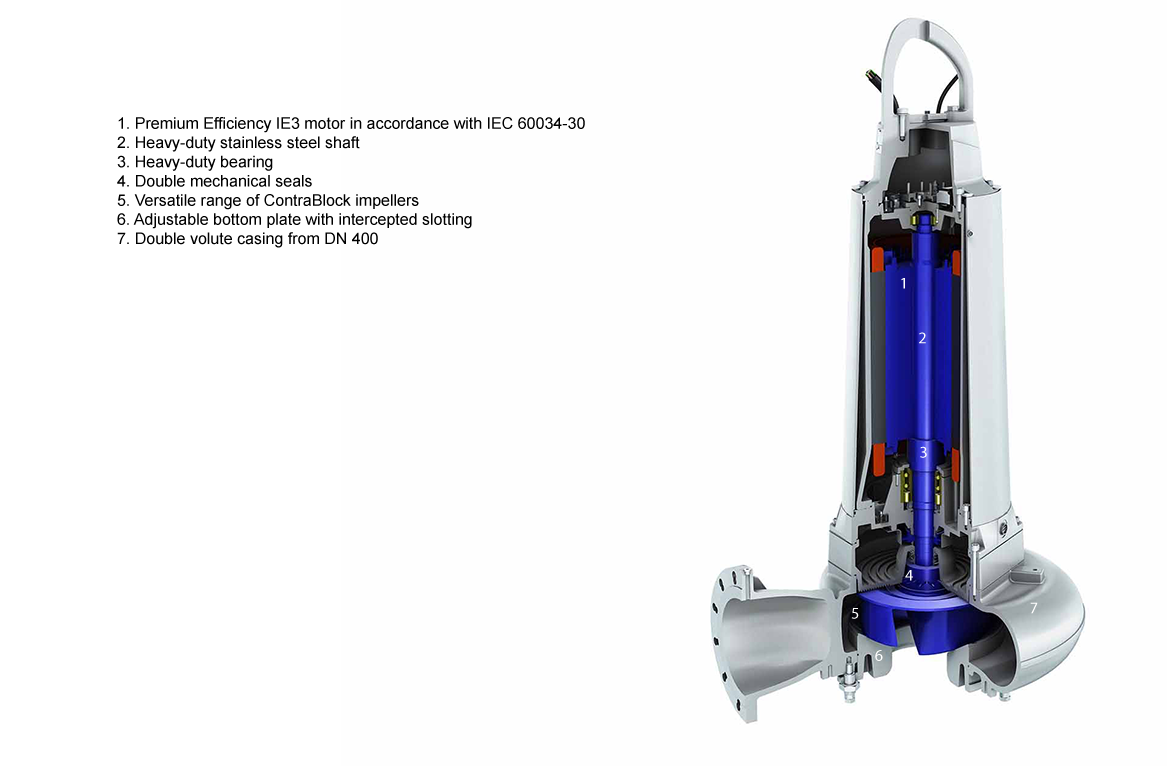
Versatile range of ContraBlock Plus impellers
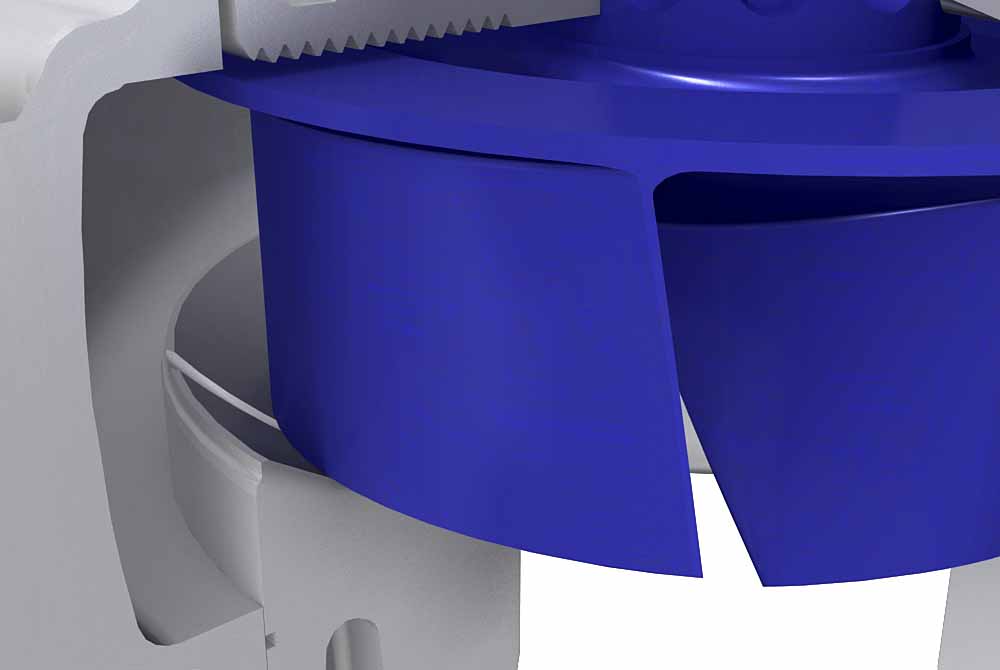
- This technology has been specially engineered to handle tough requirements, such as reduced water consumption and higher rag and solid content
- Highly reliable and efficient impeller design with single and multi-vane models to ensure exceptional blockage resistance.
- Optimum balance of impeller vane numbers and solids handling, based on extensive Computational Fluid Dynamics (CFD) research and testing
- Market leading efficiency, without compromising on solid size and rag handling
Adjustable bottom plate with intercepted slotting
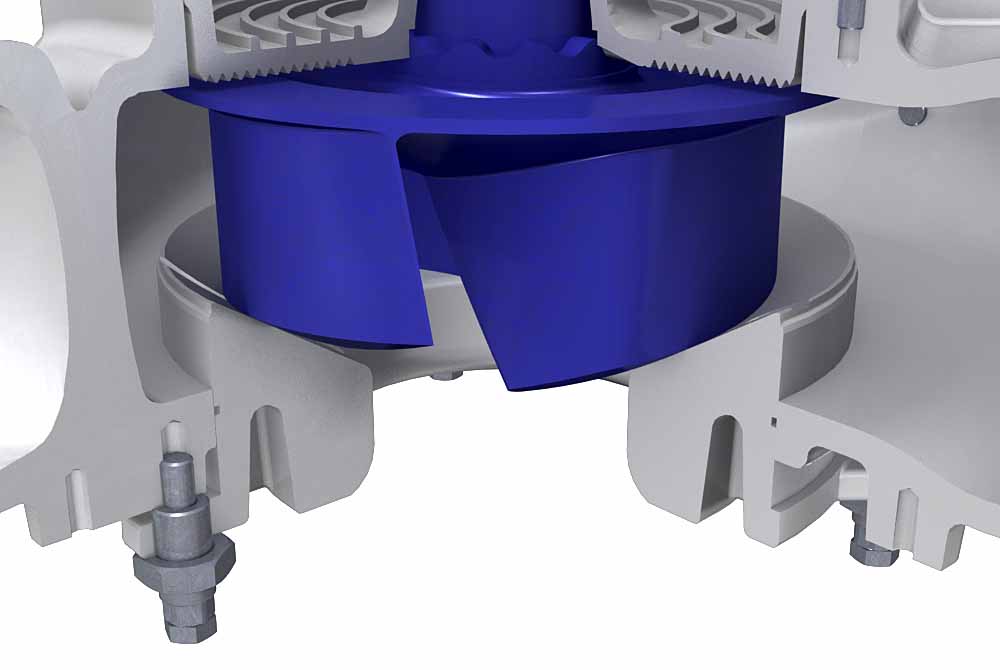
- Significant energy savings throughout lifetime
- Blockage free operation
- Adjustment of the bottom plate restores pump efficiency
- Maintains efficient rag handling throughout its lifetime
Double volute casing from DN 400
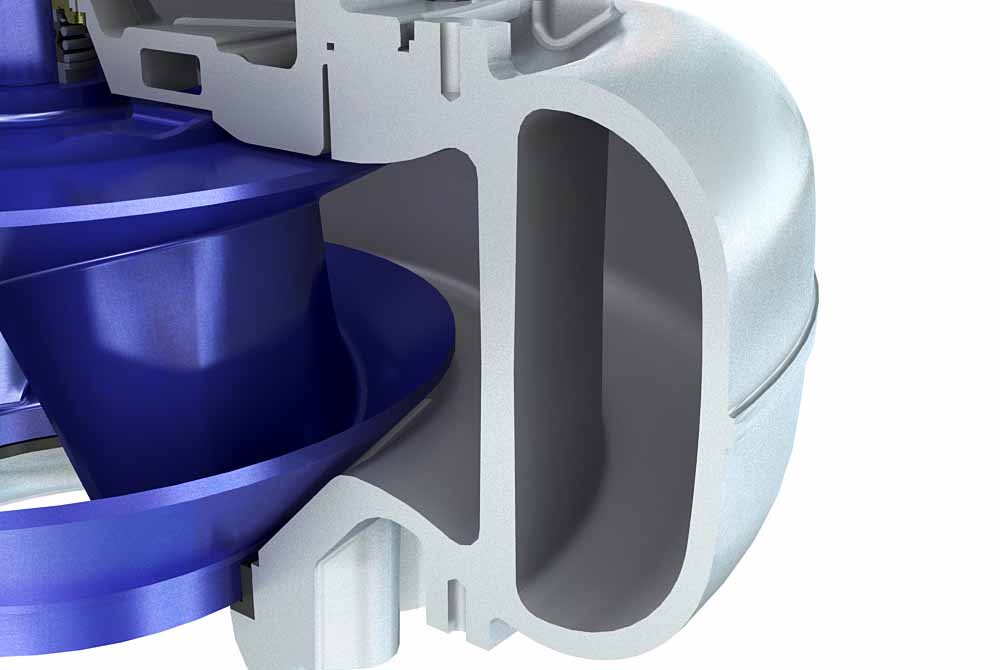
- Reduces radial forces and shaft deflection
- Maximizes the life of bearings and shaft seals, thereby reducing lifecycle costs
Double mechanical seals
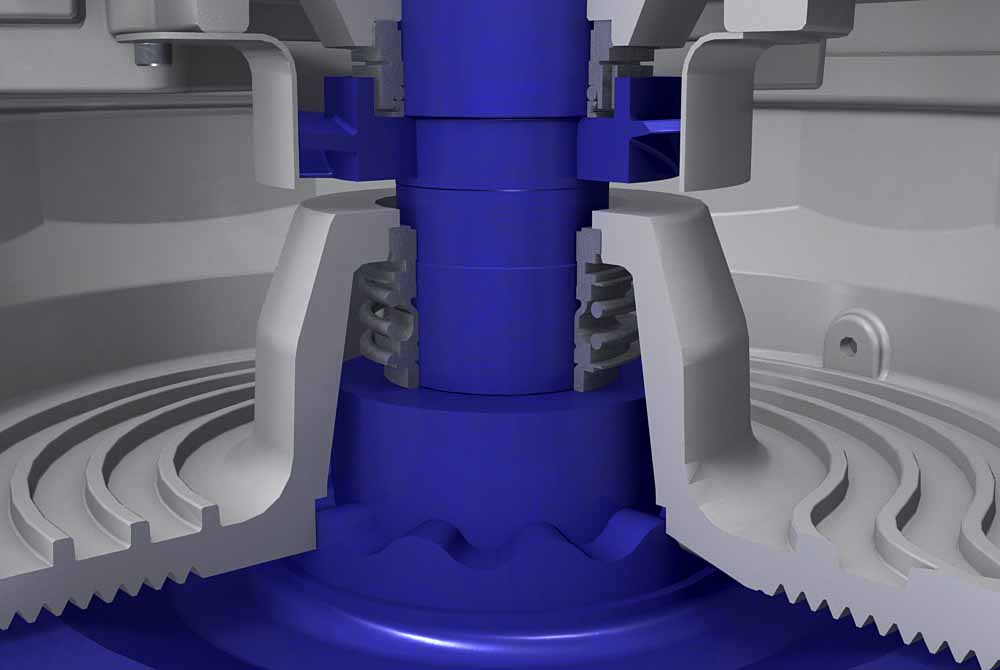
- Silicon carbide/silicon carbide (SiC/SiC) provides maximum resistance from abrasives
- Seal blockage prevention reduces operational costs
- SiC/SiC is chemically resistant in wastewater and most other industrial applications
Heavy-duty stainless steel shaft
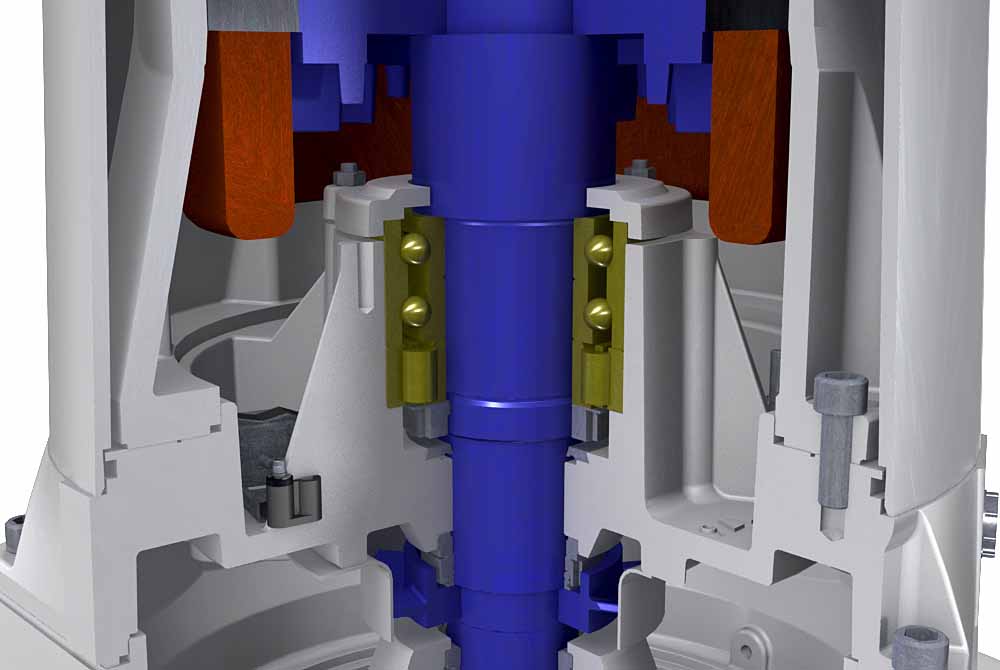
- Minimizes deflection at mechanical seal to <0.05 mm/0.002 inches
- Increased safety against fatigue fractures
Heavy-duty bearing
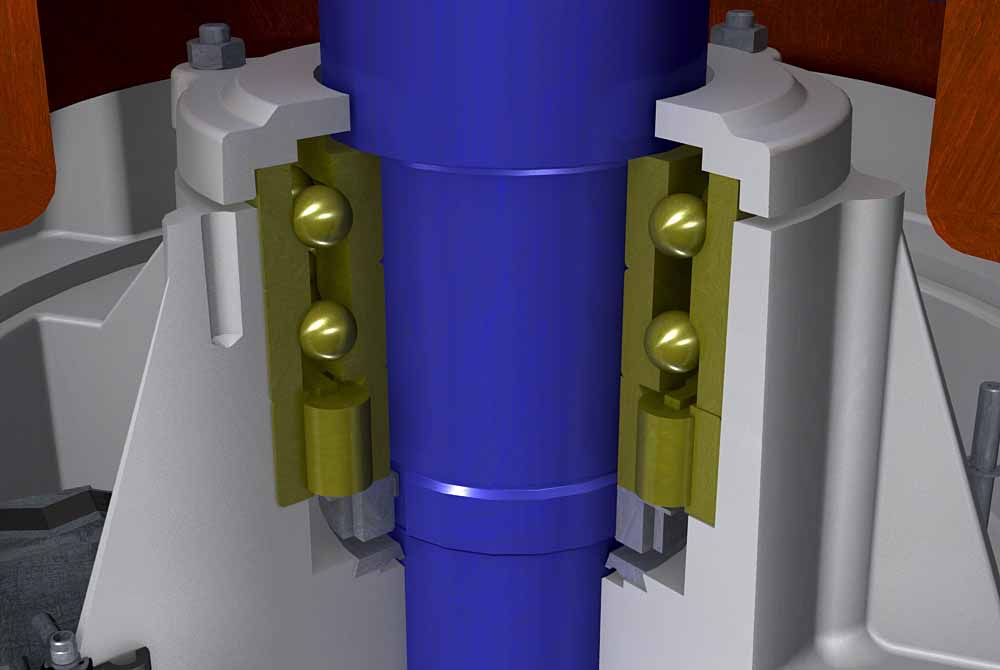
- Minimum life 50'000 h for motors up to 9 kW and minimum 100'000 h for motors larger than 11 kW
Premium Efficiency IE3 motor in accordance with IEC 60034-30
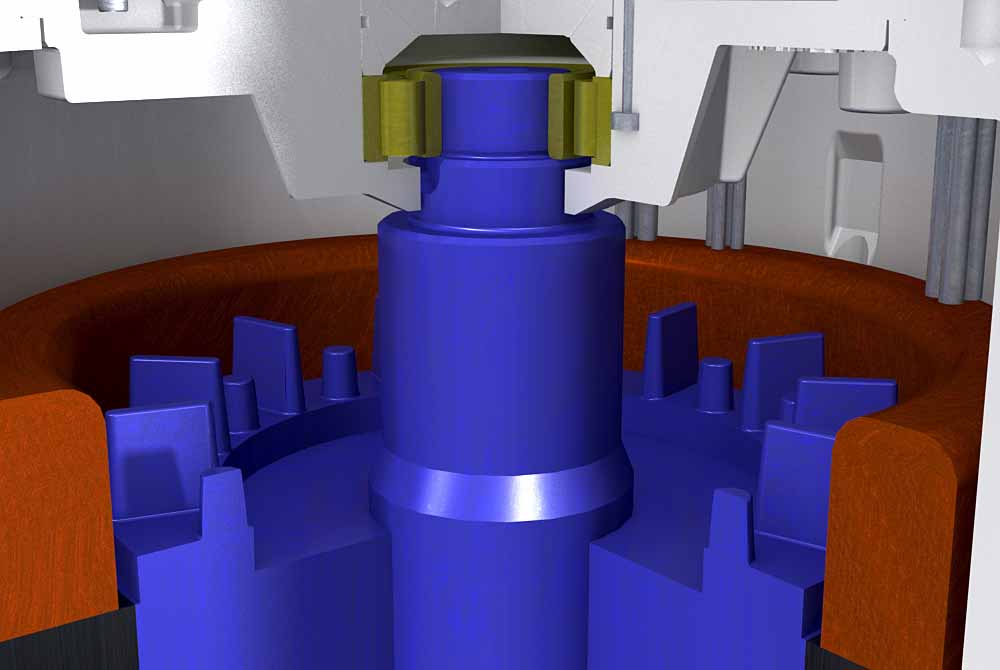
- Premium Efficiency motors in accordance with IEC 60034-30. Level IE3 with testing in accordance with IEC60034-2-1
- Designed for Variable Frequency Drive (VFD) operation.
- ATEX, FM and CSA certified motors available as option. Versatile types of sensors optional available, such as for thermal, moisture and vibration detection.
- Significant carbon footprint reduction and increased lifetime by low winding temperature rise
Versatile range of ContraBlock Plus impellers
- This technology has been specially engineered to handle tough requirements, such as reduced water consumption and higher rag and solid content
- Highly reliable and efficient impeller design with single and multi-vane models to ensure exceptional blockage resistance.
- Optimum balance of impeller vane numbers and solids handling, based on extensive Computational Fluid Dynamics (CFD) research and testing
- Market leading efficiency, without compromising on solid size and rag handling
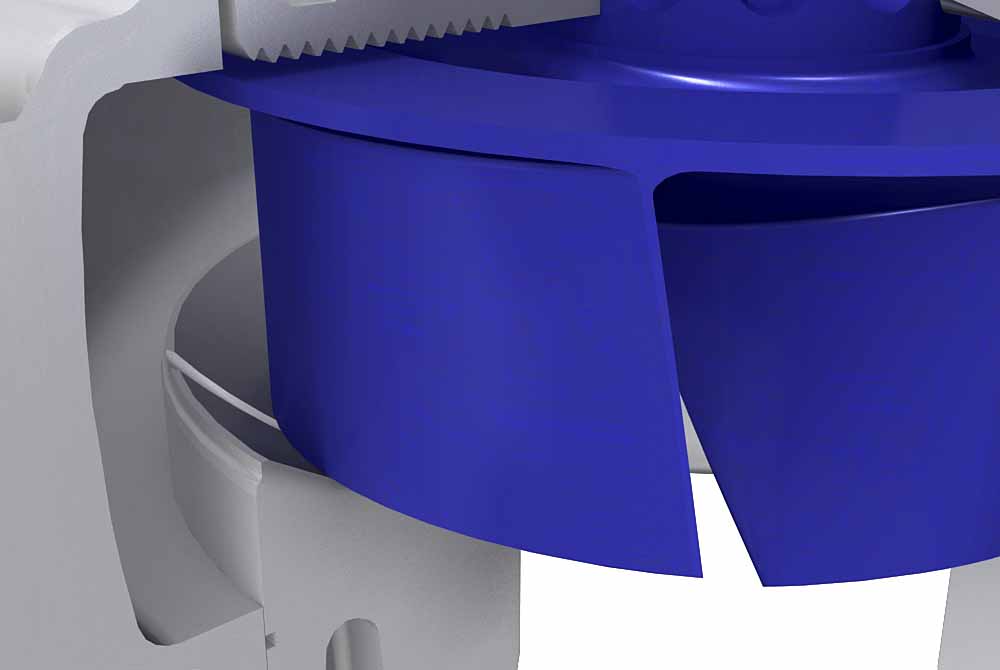
Adjustable bottom plate with intercepted slotting
- Significant energy savings throughout lifetime
- Blockage free operation
- Adjustment of the bottom plate restores pump efficiency
- Maintains efficient rag handling throughout its lifetime
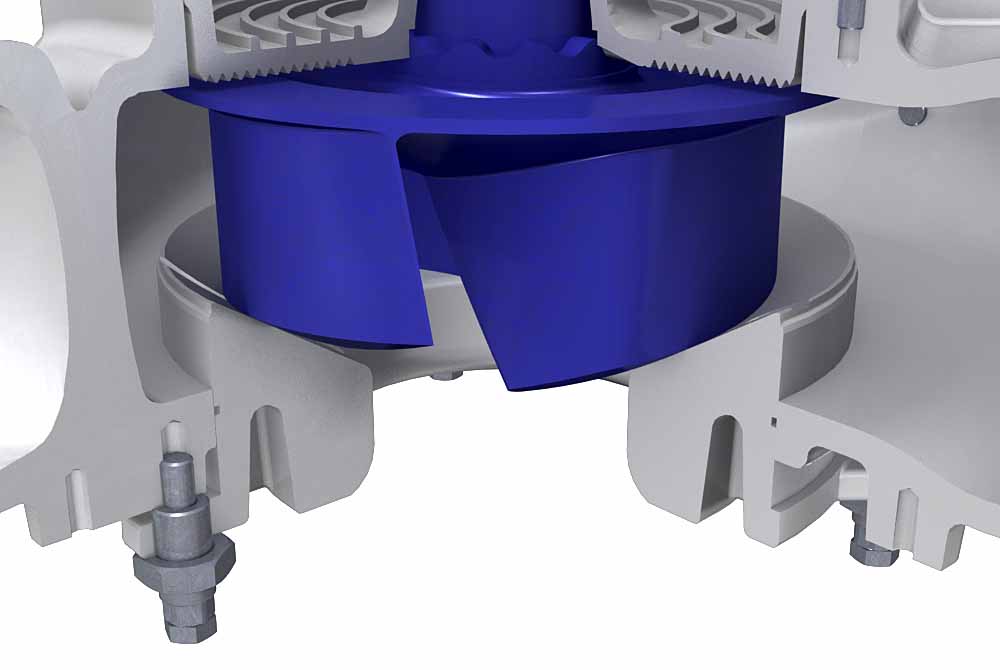
Double volute casing from DN 400
- Reduces radial forces and shaft deflection
- Maximizes the life of bearings and shaft seals, thereby reducing lifecycle costs
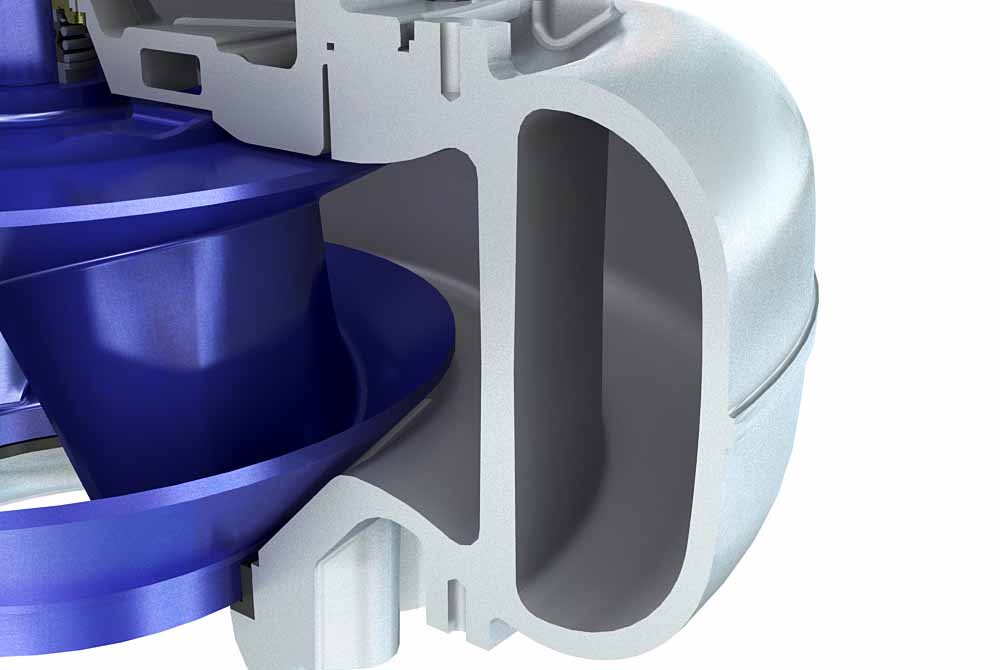
Double mechanical seals
- Silicon carbide/silicon carbide (SiC/SiC) provides maximum resistance from abrasives
- Seal blockage prevention reduces operational costs
- SiC/SiC is chemically resistant in wastewater and most other industrial applications
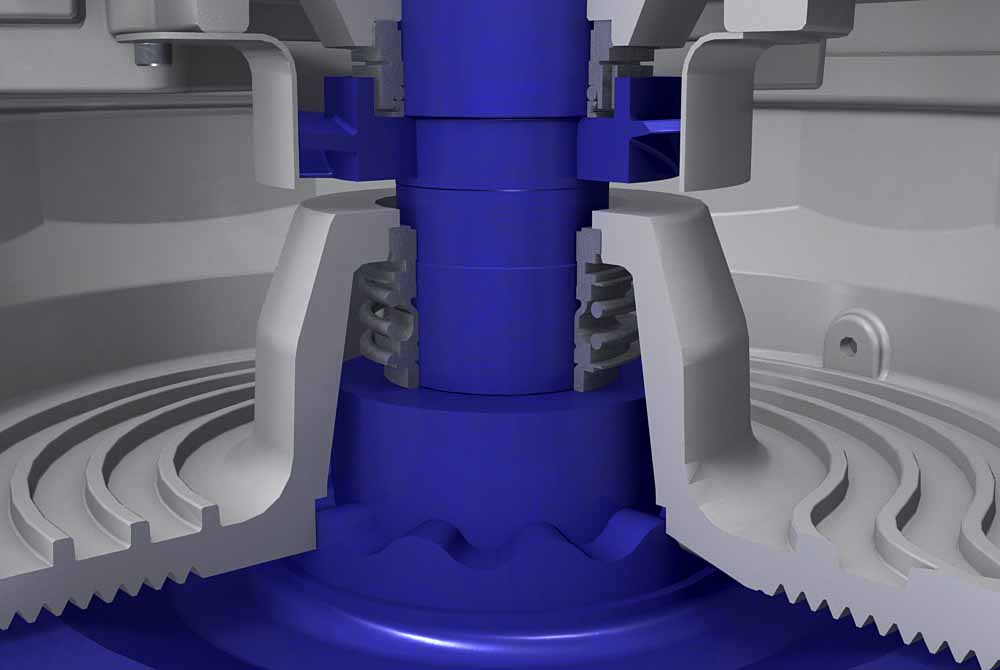
Heavy-duty stainless steel shaft
- Minimizes deflection at mechanical seal to <0.05 mm/0.002 inches
- Increased safety against fatigue fractures
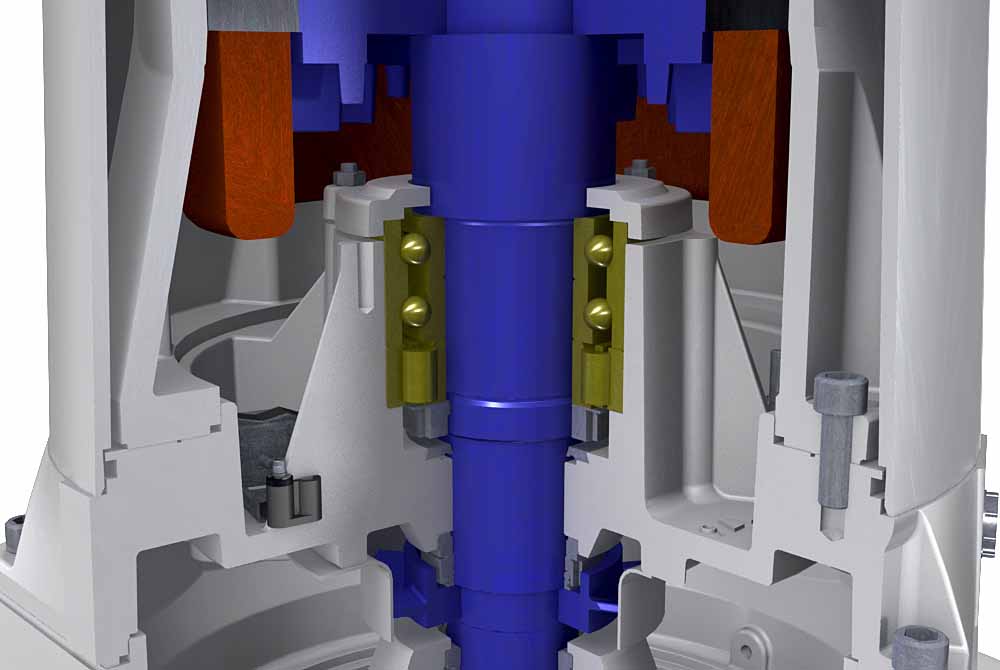
Heavy-duty bearing
- Minimum life 50'000 h for motors up to 9 kW and minimum 100'000 h for motors larger than 11 kW
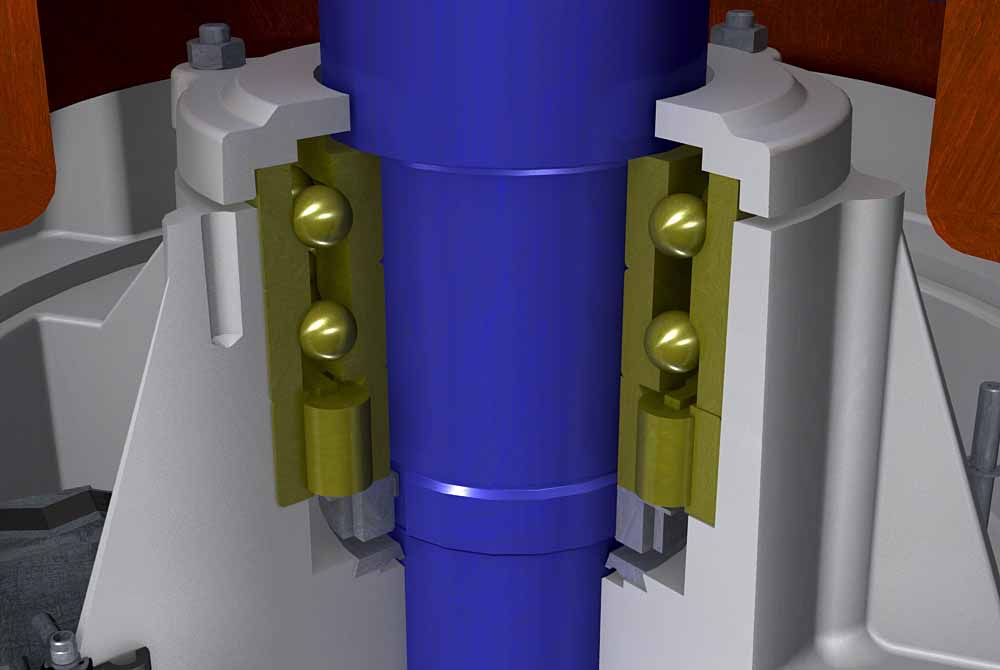
Premium Efficiency IE3 motor in accordance with IEC 60034-30
- Premium Efficiency motors in accordance with IEC 60034-30. Level IE3 with testing in accordance with IEC60034-2-1
- Designed for Variable Frequency Drive (VFD) operation.
- ATEX, FM and CSA certified motors available as option. Versatile types of sensors optional available, such as for thermal, moisture and vibration detection.
- Significant carbon footprint reduction and increased lifetime by low winding temperature rise
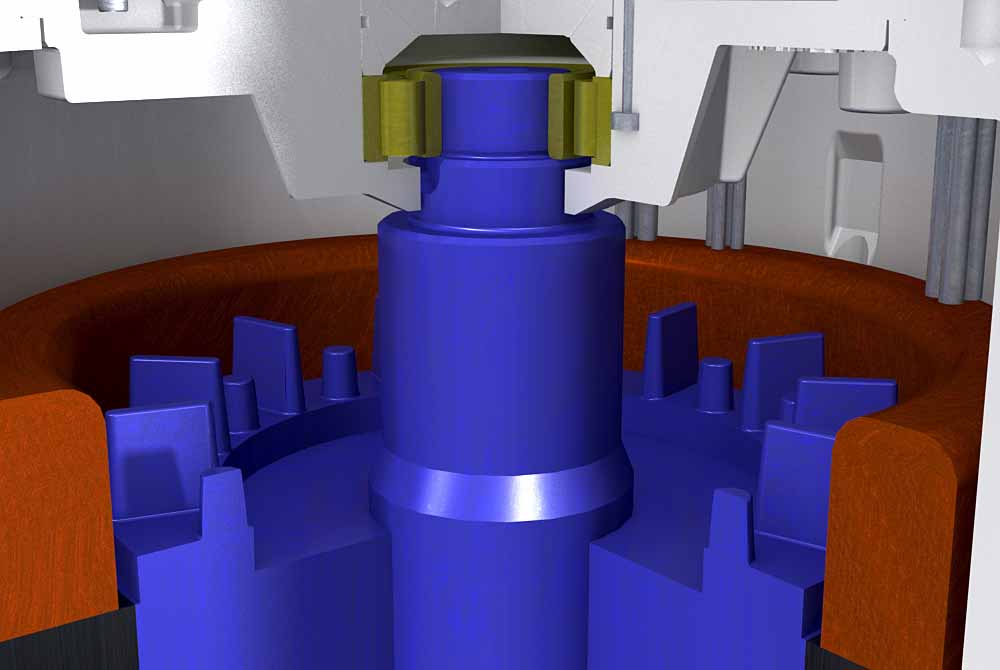
Talk or write to our experts to find your best solution.